Large-scale industrial production of wood pellets from hard and soft wood in premium quality.
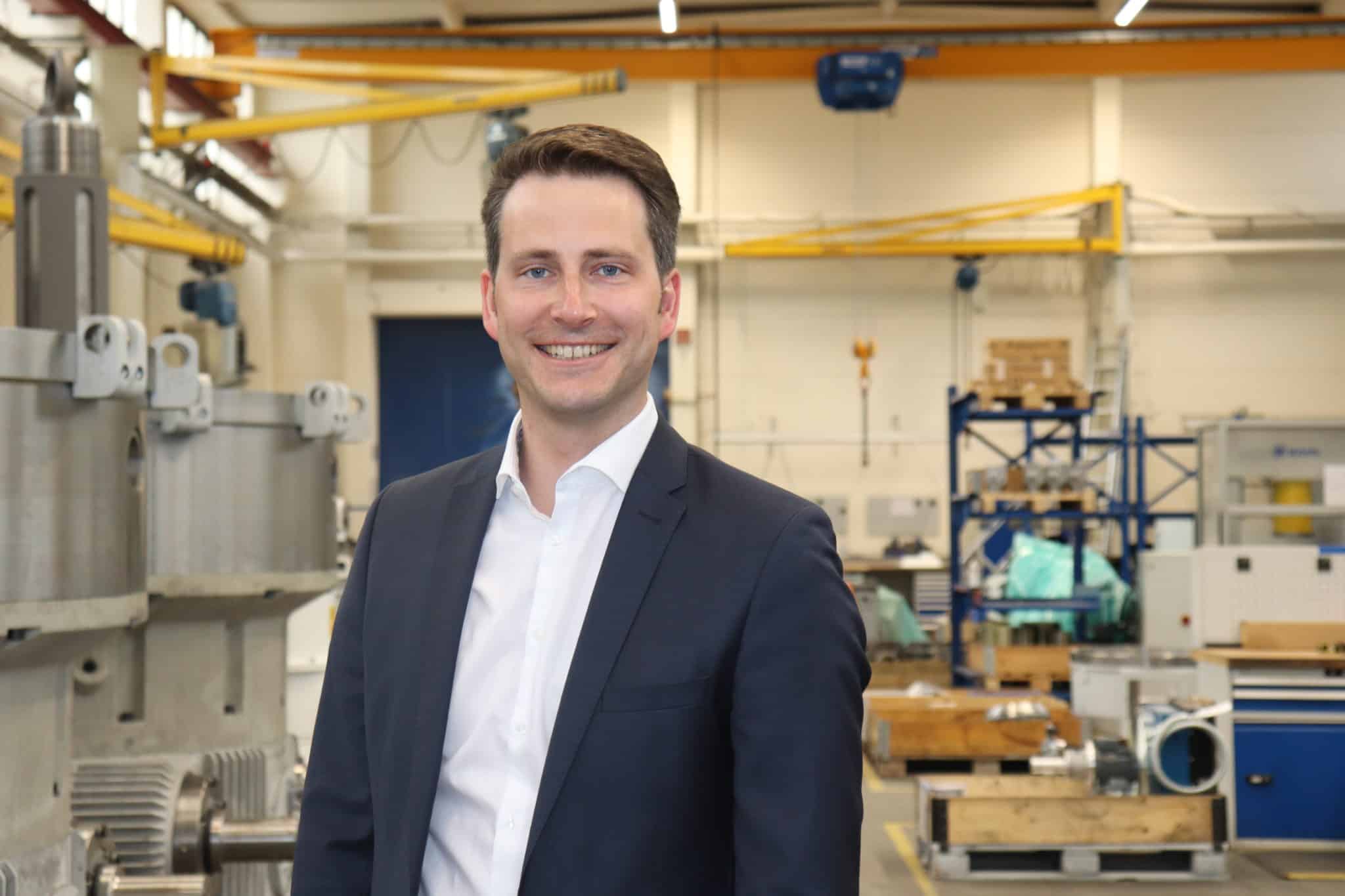
Over the past decades, the production of wood pellets has required the highest level of engineering skill and numerous failed attempts to achieve today’s standards. While softwood was used for the production of wood pellets at the end of the 1990s, producers today hardly encounter any limitations with regard to the raw components that can be used. The reason for this is a technically highly sophisticated pelleting press. Thanks to the flat die technology, the German machine manufacturer AMANDUS KAHL has revolutionized the market with the pelleting press 65-1500. This flat die pelleting press meets the requirements of large-scale industry. From a repertoire of over 16 different pelleting presses, almost all industries can now be equipped with the right solution. Particularly for the pelleting of wood, AMANDUS KAHL has developed pelleting presses which comply with the harsh requirements of wood pelleting due to their reinforced design and various other construction details.
No other company manufactures flat die pelleting presses with which – depending on the type of wood – up to 12 tons of wood pellets can be produced per hour. For several decades, these have proven themselves through their robust design, economic efficiency and quiet operation. The raw material wood in particular depends on a variety of optimum technical conditions to convert it into high-quality pellets. When processing wood chips and other shredded wood, a solid design and high availability are prerequisites for uninterrupted continuous operation.
For many years KAHL pelleting presses have been used in large-scale wood-processing industries worldwide. KAHL flat die pelleting presses are used from Brazil via the USA to Europe and Russia. Plants that produce from 200 to 800,000 tons of wood pellets per year are equipped with these presses. The youngest member of the KAHL pelleting press family – the flat die pelleting press type 65-1500 – is responsible for this range of capacities. With a die diameter of 1500 millimetres it is also the largest press of AMANDUS KAHL.
The KAHL Flat Die Technology
Numerous KAHL flat die pelleting presses are suitable for the pelleting of wood, which only differ in their throughput capacity. In addition to the 65-1500, customers worldwide also use presses of the types 37-850, 39-1000, 45-1250, 60-1250, 60-1500 and 65-1250.
The technical design of all flat die pelleting presses from AMANDUS KAHL is identical. This includes in particular the pan grinder head with the respective rollers and the flat die, which has become a unique selling point on the market due to its robustness.
As a result of horizontal agglomeration by compression and vertical product supply, the KAHL process appropriates the force of gravity. The product is fed by means of a suitable feeding screw and the product is distributed vertically in free fall, which means that an additional mechanical device for feeding is not required. Due to the large press interior, even voluminous products find sufficient space. After only a short time, a product layer is formed on the flat die, which is then rolled over by the pan grinder rollers, which press the product into the holes of the die. The automatic control system DISTAMAT by AMANDUS KAHL ensures continuous adjustment and control of the roller gap, so that a uniform pellet production is possible even with inconsistent product supply. After leaving the die at the lower side, the pellets are cut to the desired length by means of height-adjustable knives.
Wood: the Mechanical Challenge in Pelleting
Compared to other products, wood has low binding strength. Besides, the sliding properties are poor. Therefore, a high frictional force builds up very quickly within the effective bores, which is also required to pellet this product with its low inherent binding properties. The moisture content in the shredded wood should be kept between 12 and 15 percent because of the pressure and bending strength, which increases as a result.
Due to the large volume reduction when compacting wood and wood shavings, particularly sawdust from about 100 to 600 kg/m³, the capacity of the machine, i.e. the press interior, must be as large as possible. This challenge also prompted AMANDUS KAHL to build the largest KAHL pelleting press to date, the press 65-1500. Special features of this new press are a high throughput capacity with the lowest possible specific energy consumption – combined with long service life and low wear costs.
Hardly any other product enters the pelleting process with such different conditions as the natural product wood: Hardwoods such as beech or oak, for example, require higher pressing forces than softwoods or conifers such as lime or spruce. Therefore the energy consumption ranges between 40 and 60 kWh/t. In addition, the high frictional resistance and low binding forces (lignin) of some types of wood make preconditioning indispensable. This can easily be achieved by the KAHL mixing conditioner, which allows to add steam, water, and other substances before pelleting.
Technical Features You Can Rely On
In recent years, AMANDUS KAHL has discovered that minor changes in the technical features of wood pelleting machines result in the production of pellets of even higher quality with less abrasion and a higher pellet hardness. For example, a pan grinder head with guide plates for the exact product distribution is installed in the KAHL presses. In addition, the presses are equipped with reinforced cutting devices, breathing air filters preventing moisture inside the gear, reinforced press bodies and pan grinder head stops for optimum adjustment of the pan grinder rollers and die. Furthermore, the KAHL pelleting presses are provided with gear oil spraying systems to protect them against overheating, with large bearings for longer service lives, and with roller shells for lower material consumption for wear parts.
AMANDUS KAHL supplies the latest technical know-how and finds the right solution together with customers from different industries. The owner-managed company, based in Reinbek, Northern Germany, looks back on more than 140 years of existence and has developed a unique selling point on the international economic market with its flat die presses. The machine range also includes pan grinder mills for energy-efficient crushing of wood, expanders, extruders, crushing roller mills, proportioning and mixing units and much more.
Are you interested in a machine from AMANDUS KAHL or are you already a KAHL customer? Then find out more on the new website at www.akahl.de, visit our online shop at www.shop.akahl.de or contact us:
AMANDUS KAHL GmbH & Co. KG
- Dieselstraße 5-9
- 21465 Reinbek
- Germany
- E-mail: info@akahl.de
- Phone: +49(0)40727710
- Fax: +49(0)4072771100